Product overview
CATIA is a leading CAD/CAM/CAE software solution for product design and innovation. It is used in a wide range of industries, including aerospace, automotive, and industrial machinery, for designing complex 3D models and simulations.Operating Systems
Windows
Data Storage
On-Premises Storage
Cloud Storage
Industry served
Automotive |
Aerospace |
Robotics & Automation |
Energy |
Defence |
Construction Equipment |
Offshore & Marine |
Education & Research |
Medical/ Healthcare |
Consumer Products |
Consumer Electronics |
Heavy Machineries |
Plastic Products |
Rail Industry |
|
|
|
|
|
|
|
3D CAD Capabilities
Parametric Modeling
Parametric Modeling: A technique where the geometry of a design is driven by parameters, such as dimensions or constraints, allowing for easy adjustments and updates to the design by altering these values
|
Assembly Modeling
Assembly Modeling: The process of creating a virtual assembly by combining individual parts or components, facilitating the simulation of how these parts fit and interact with each other
|
Stress Analysis
Stress Analysis: The evaluation of static or dynamic stress on materials under external forces or loads to ensure the design meets required strength and durability criteria
|
Sheet Metal Design
Sheet Metal Design: Dedicated tools for designing components intended to be fabricated from sheet metal, incorporating features like bends, folds, and cuts
|
Surface Modeling
Surface Modeling: The creation of complex surfaces with high-quality finishes, suitable for designs where aesthetics and freeform shapes are key
|
Structure Member Design
Structure Member Design: Tools for designing structural elements, focusing on their material properties, cross-sectional dimensions, and the support they provide within the context of the entire structure
|
Drawing and Detailing
Drawing and Detailing: The generation of detailed 2D drawings from 3D models, providing all necessary information for manufacturing, including dimensions, tolerances, and notes
|
Tool and Die Design
Tool and Die Design: Specialized functionalities for designing manufacturing aids such as molds, dies, and fixtures, optimizing them for production processes
|
Routing & Piping
Routing & Piping: Tools to design and simulate the routing of electrical cabling, hydraulic or pneumatic tubing, and piping systems within a model
|
Motion Simulation
Motion Simulation: The simulation of movement within an assembly to analyze the mechanical interactions and ensure the design functions as intended
|
Part Libraries
Part Libraries: Access to pre-designed part catalogs, allowing designers to incorporate standard or commonly used components into their designs
|
Flexible File Formats
Flexible File Formats: Support for a wide range of file formats, ensuring interoperability between different CAD systems and facilitating collaboration
|
Configurations & Design Variants
Configurations & Design Variants: The ability to create multiple versions of a part or assembly within the same file, simplifying the management of design variations
|
Equation/Formula Driven Design
Equation/Formula Driven Design: Incorporating mathematical equations or formulas to drive design changes, enabling complex relationships between design elements
|
Excel Driven Configurations
Excel Driven Configurations: The use of Excel spreadsheets to manage design parameters, allowing for the easy manipulation of large sets of data to drive design variations
|
Collaboration
Flexible File Formats: Support for a wide range of file formats, ensuring interoperability between different CAD systems and facilitating collaboration
|
File Compatibility
File Compatibility: Ensuring designs can be accessed and modified across different software platforms, enhancing flexibility in the design process
|
Collision Detection
Collision Detection: The ability to detect when two or more components in a design occupy the same physical space, preventing potential assembly issues
|
Interference/Overlap Detection
Interference/Overlap Detection: Tools to identify parts within an assembly that interfere with each other, crucial for verifying the feasibility of assembly and operation
|
CAM Integration
CAM Integration: Seamless integration with Computer-Aided Manufacturing processes, allowing for direct transition from design to production
|
3D Model Annotation
3D Model Annotation: Adding notes, dimensions, and technical data directly on 3D models, facilitating communication and understanding of design intent
|
Automated Task Scheduling
Automated Task Scheduling: Automation of repetitive or time-consuming tasks within the design process, improving efficiency and accuracy
|
Costing (Parts)
Costing (Parts): Estimation tools for analyzing the cost of individual components, considering materials, manufacturing processes, and other factors
|
Costing (Assembly)
Costing (Assembly): The ability to estimate the overall cost of assembling a product, taking into account all parts and labor involved
|
Design Standards Validator
Design Standards Validator: Tools to automatically check designs against predefined industry standards or company-specific guidelines, ensuring compliance
|
Patterns Compatibility
Patterns Compatibility: Support for creating and manipulating patterns in designs, such as holes, pockets, or decorative features, to ensure consistency and reduce manual effort
|
API Customization
API Customization: Providing a programming interface for users to develop custom functions or integrate third-party tools, enhancing software flexibility
|
Sculpting/Freeform Modeling
Sculpting/Freeform Modeling: Tools for creating organic shapes and complex geometries that are difficult to achieve with traditional modeling techniques
|
Visualization & Rendering
Visualization & Rendering: Generating high-quality images or animations from 3D models, useful for presentations, marketing, or design verification
|
Assembly Analysis and Visualization Tools
Assembly Analysis and Visualization Tools: Advanced functionalities for analyzing and visualizing the mechanical performance and assembly sequence of products, aiding in the identification of potential issues and the optimization of the design
|
2D Drafting Capabilities
Associativity
Associativity: Ensures that changes made in the 3D model are automatically reflected in the related 2D drawings, maintaining consistency and accuracy across documents
|
Dimensions & Annotation
Dimensions & Annotation: Tools for adding dimensions (linear, radial, angular, etc.) and annotations (text notes, symbols) to drawings, essential for communicating design intent and specifications
|
BOM (Bill of Materials)
BOM (Bill of Materials): Automatically generates a detailed list of parts, assemblies, and materials required to build a product, including quantities and other properties, directly from the 3D model
|
Exploded Views
Exploded Views: Illustrates an assembly or system with its components slightly separated from their operational positions, useful for assembly instructions or maintenance manuals
|
Section Views
Section Views: Cuts through a part or assembly to show its internal features, aiding in the understanding of complex internal structures
|
Detail Views
Detail Views: Magnifies a small, intricate part of a drawing to show fine details more clearly, often with a higher level of annotation
|
Layer Management
Layer Management: Allows the organization of different elements of a drawing into layers that can be independently controlled and visualized, improving the readability of drawings
|
Drawing Template Customization
Drawing Template Customization: Enables the creation of customized drawing templates with predefined settings, such as paper size, title blocks, and border information, ensuring consistency across documentation
|
Multiple Drawing Sheets
Multiple Drawing Sheets: Supports the creation of documents with multiple sheets within a single file, facilitating the organization and management of complex drawing sets
|
Hole Tables
Hole Tables: Summarizes all holes (and often other features) in a part or assembly, listing dimensions, locations, and other specifications in a tabulated form for easy reference
|
Hole Callouts
Hole Callouts: Automatically annotates holes with dimensions and specifications directly in the drawing view, providing clear manufacturing instructions
|
Hole Series
Hole Series: Facilitates the design and documentation of a series of holes with similar characteristics, simplifying the specification process
|
GD&T
GD&T (Geometric Dimensioning and Tolerancing): A system for defining and communicating engineering tolerances through symbols, providing a clear method to express the allowable variation in form, orientation, and location of features
|
Drawing Views
Drawing Views: Standard projection views (front, top, side, etc.) and auxiliary views for representing the 3D model in 2D formats, crucial for comprehensive documentation
|
Automated View Creation
Automated View Creation: Generates standard drawing views of a 3D model automatically, saving time and ensuring consistency across drawings
|
Custom Properties
Custom Properties: Allows users to define and attach custom data to parts or drawings, such as part numbers, material specifications, or designer names, which can be automatically populated in title blocks, BOMs, and annotations
|
Rating details
Evaluation criteria
|
|
|
|
|
|
|
Technical Features
3D CAD Capabilities | ||
|
|
|
|
|
|
|
|
|
|
|
|
|
|
|
|
|
|
|
|
|
|
|
|
|
|
|
|
|
|
2D Drafting Capabilities | ||
|
|
|
|
|
|
|
|
|
|
|
|
|
|
|
|
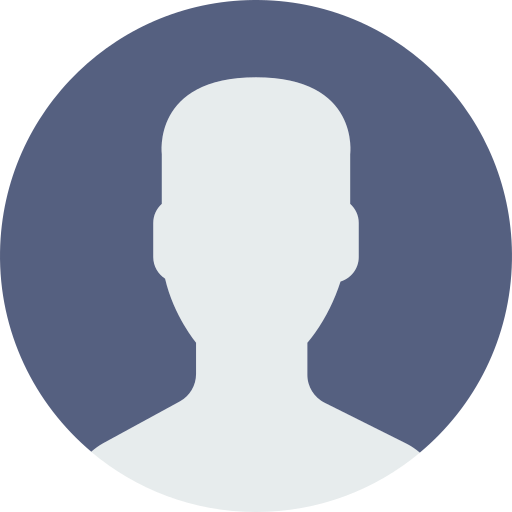
djcj
ancn
May 22 2024 04:34 pm
Year of experiance.
5
Industry used this software
sdf
Standout feature
dcs
Enhancement fields
cdsmf